The workshop
Our workshop is located on the top floor of the Claudie Pierlot fashion house. It was created there at the instigation of our founder.
Claudie Pierlot decided as early as 1984 to combine the rigour and working practices of a fashion house with the ready-to-wear sector. This approach continues to this day, allowing us to produce and offer our customers superb-quality outfits at affordable prices.
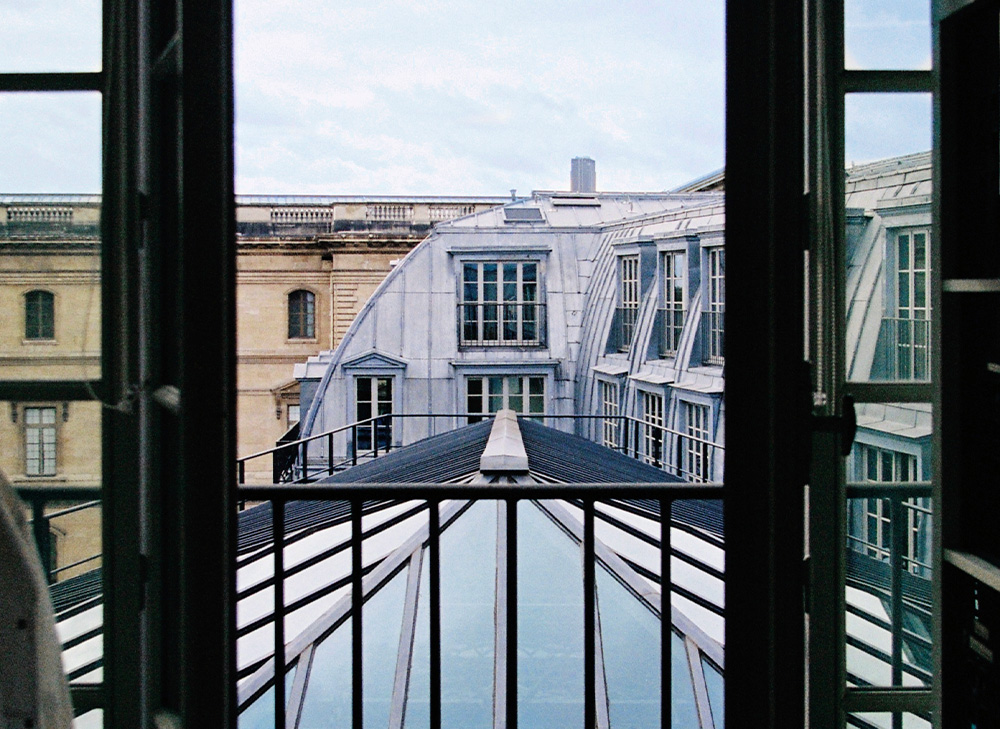
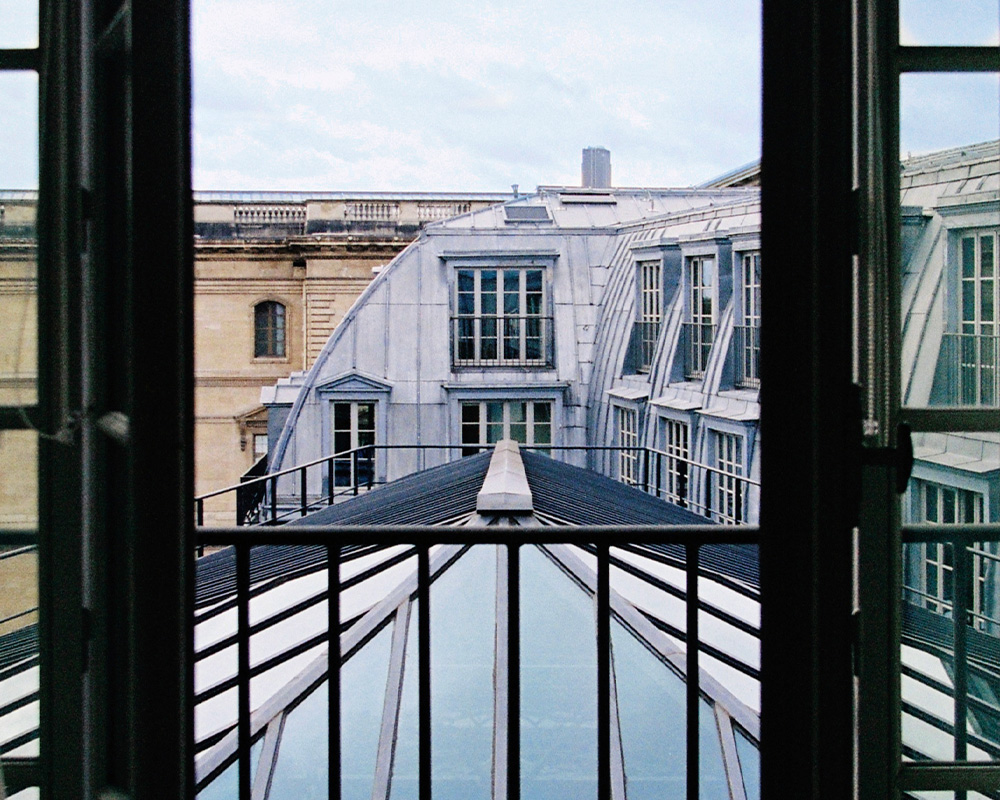
Pattern Making
Each of our pieces is created in three dimensions from a Stockman mannequin before being turned into a pattern. This approach sees clothing not as a collection of numbers or measurements but as a volume made to be worn.
Our pattern makers guarantee that the cut of the garment is just right, that it is comfortable and that it fits the body to perfection.
This method also lets them work more intuitively. Being able to touch and feel the garments, try them on several different body shapes and apply alterations if necessary before they go into mass production is a decisive factor in the final quality of our garments.
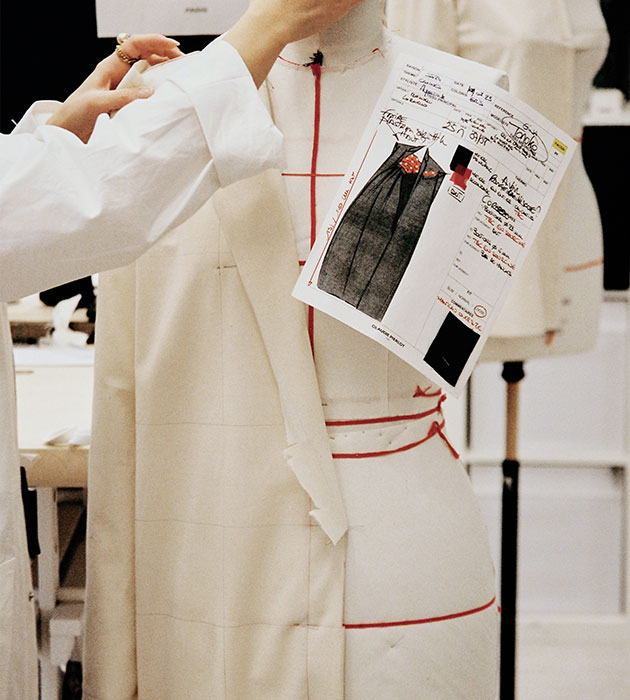
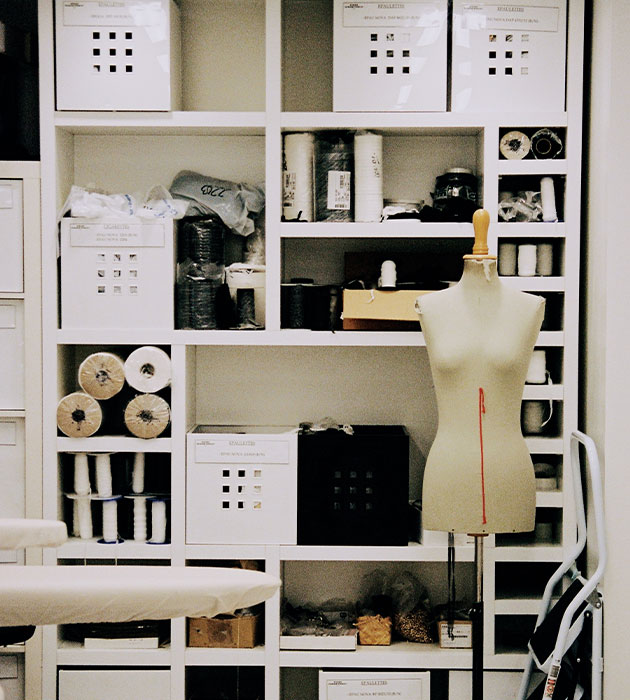
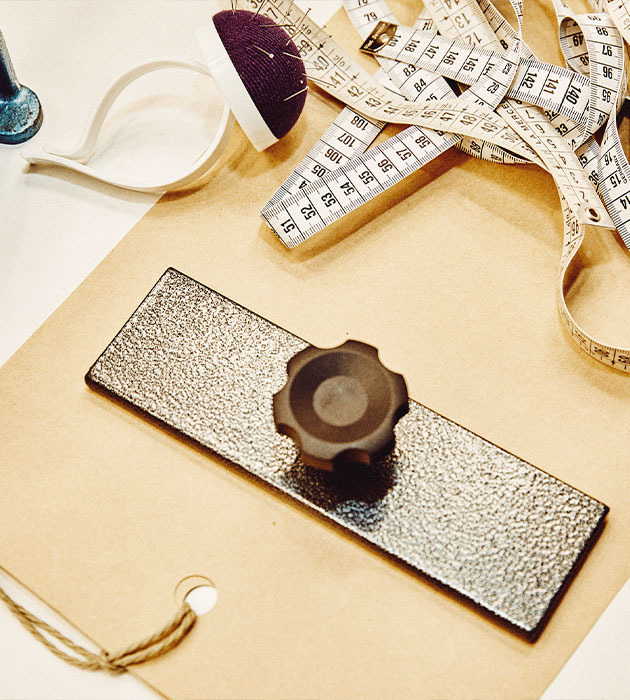
The research
laboratory
It's also not unusual for our workshop to take on the appearance of a research laboratory. Our workshop staff work in harmony with our styling team and are always keen to experiment with new approaches, like introducing new materials or cuts.
They tweak existing silhouettes to make them more more comfortable and stylish. Every day, the new discoveries they make in the workshop help to keep the Claudie Pierlot brand and its new collections fresh and up-to-date.
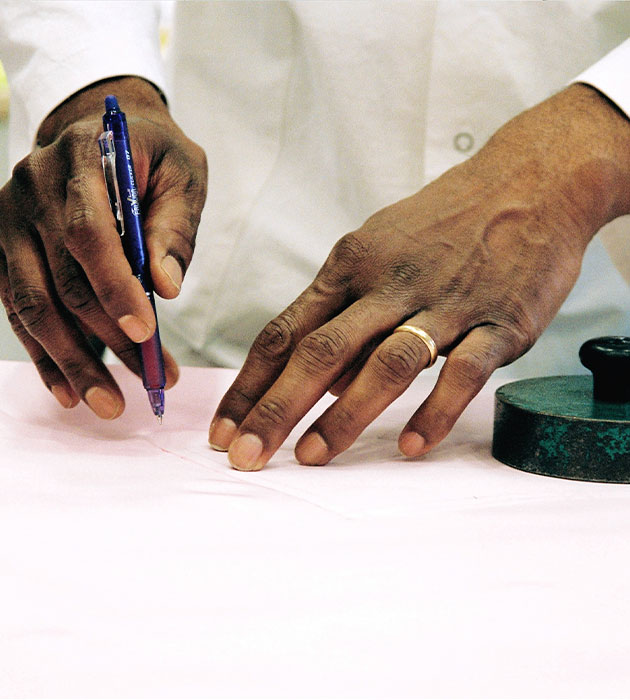
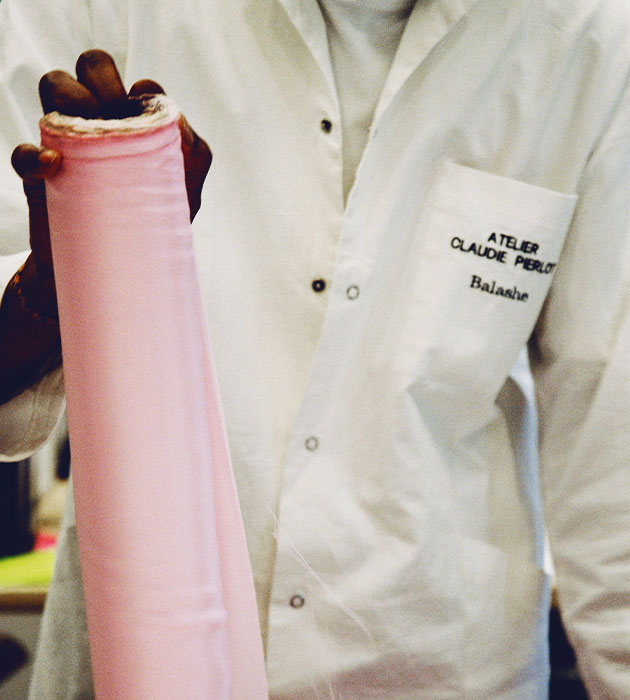
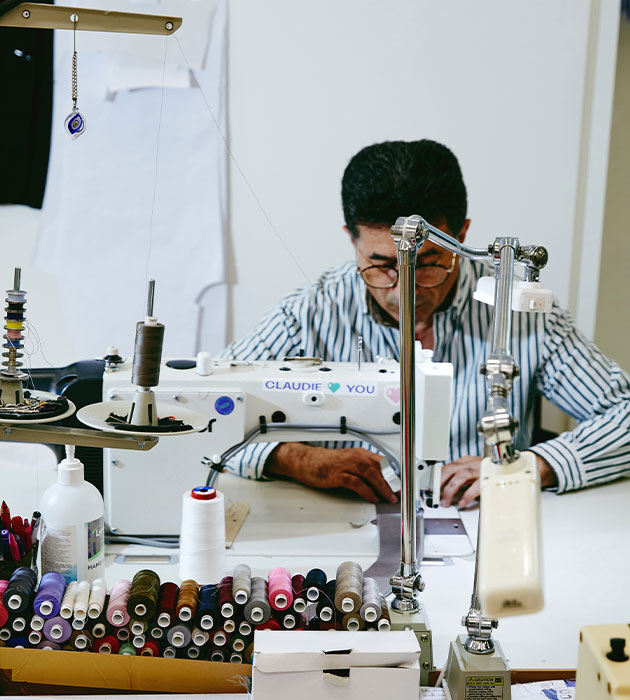
The team
Our workshop team is made up of around ten people from different backgrounds. Including pattern makers, cutters, and prototype makers, the team's combined experience has shaped the most emblematic pieces in our brand's history.
If you ask them what their secret is, they'll tell you it's just a matter of "having the knack".
Although they use modern equipment, their methods methods and expertise are purely traditional. Their technique is based on experience and repetition. This is impossible to duplicate with a machine.
The design
stages
Les Exceptions
As we celebrate our 40th anniversary this year, we've chosen to focus on our Parisian workshop: its creativity and expertise. We have called the result of this initiative "Les Exceptions".
Opting to focus on special occasion outfits, , the skilled artisans in our workshop have designed exclusive pieces whose apparent elegance lends itself perfectly to the spotlight. The delicate drape of a dress, the moiré effect of a suit and a bustier worked like a corset all bear witness to their experience and expertise.
Find them in our shops
- Cannes
- Monaco
- Galeries Lafayettes Haussmann
- Pierre-charron
- Saint-germain
- Genève
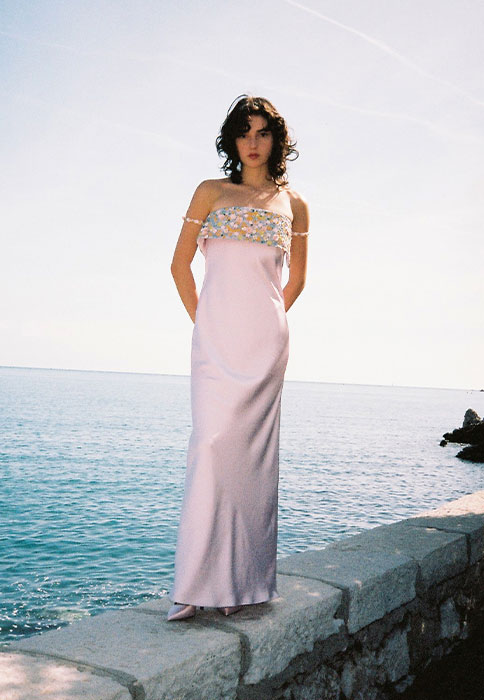
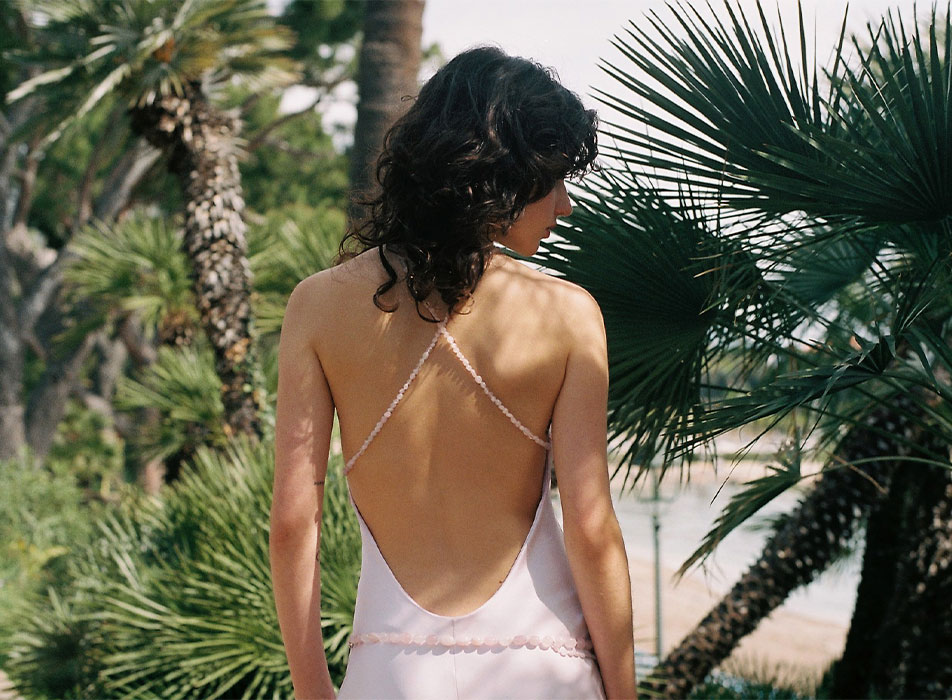
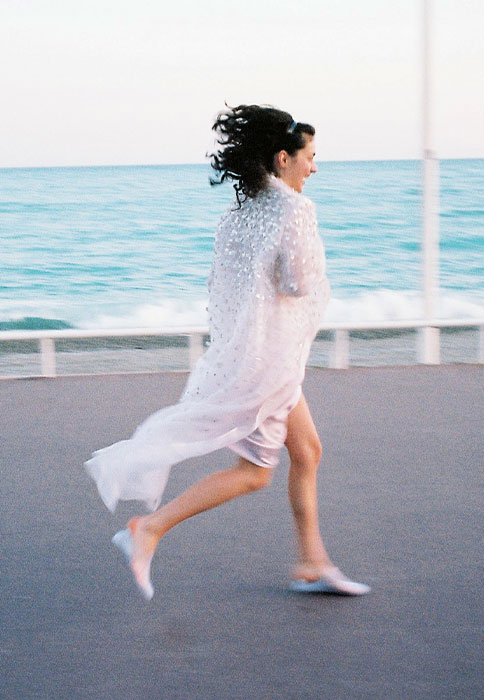
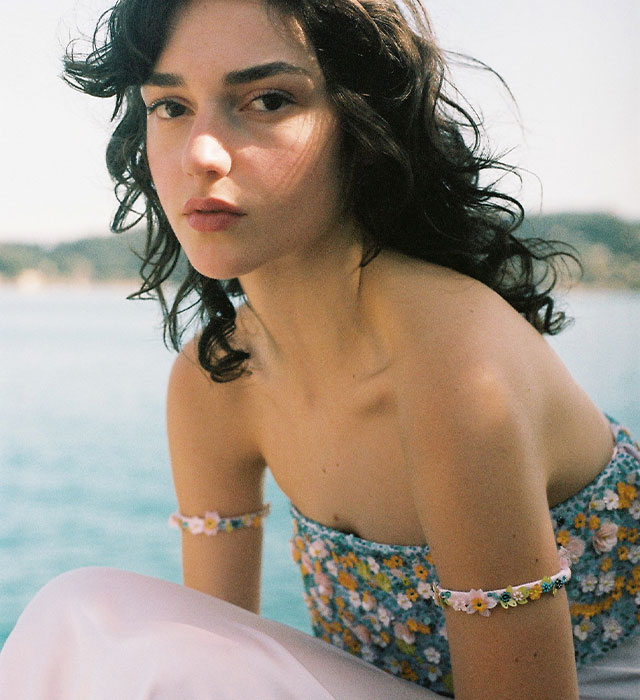
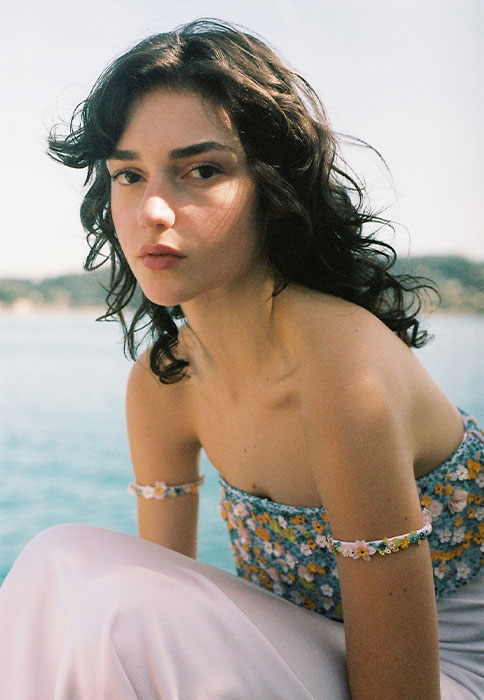
The "Les Exceptions"
capsule
illustrates the union
between fashion,
beauty and craftsmanship.
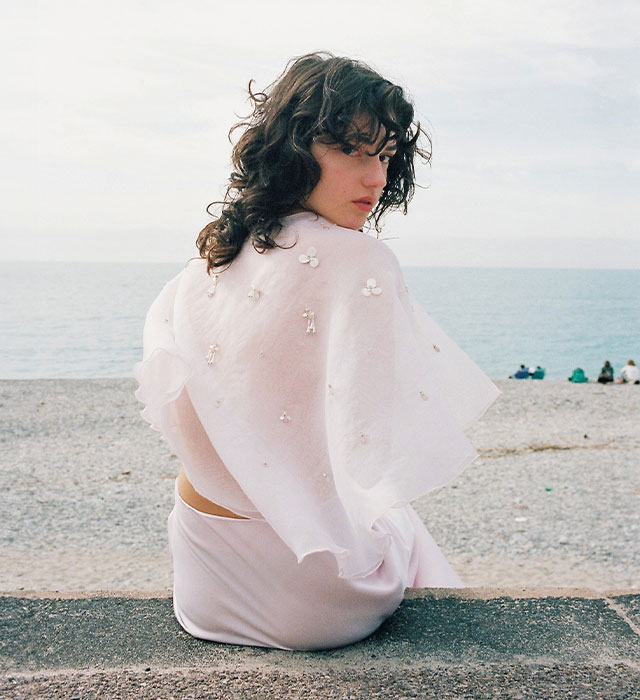
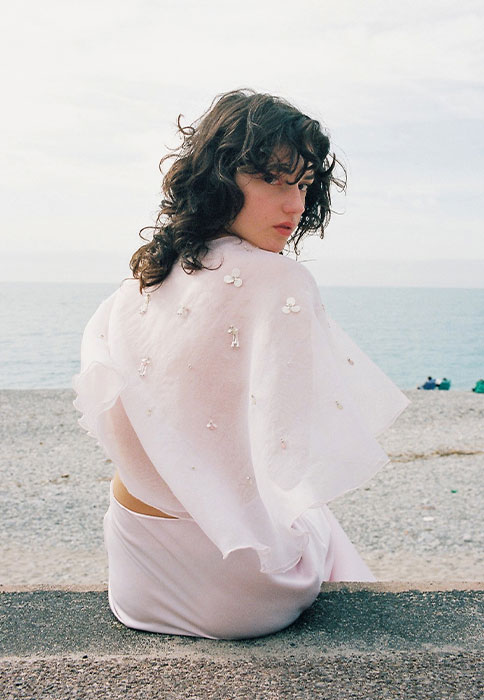
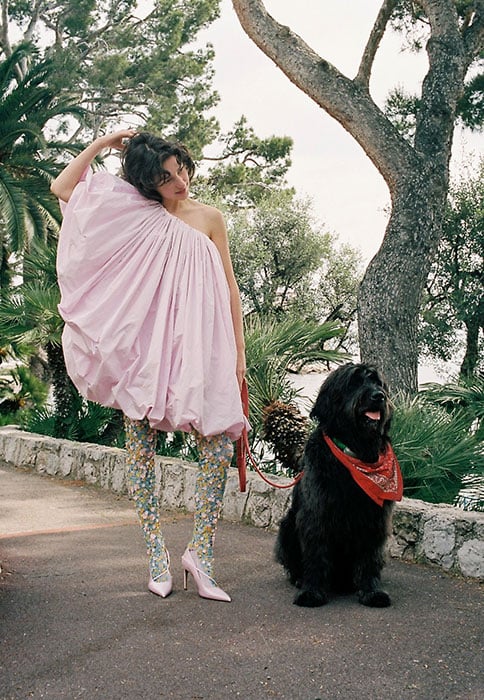
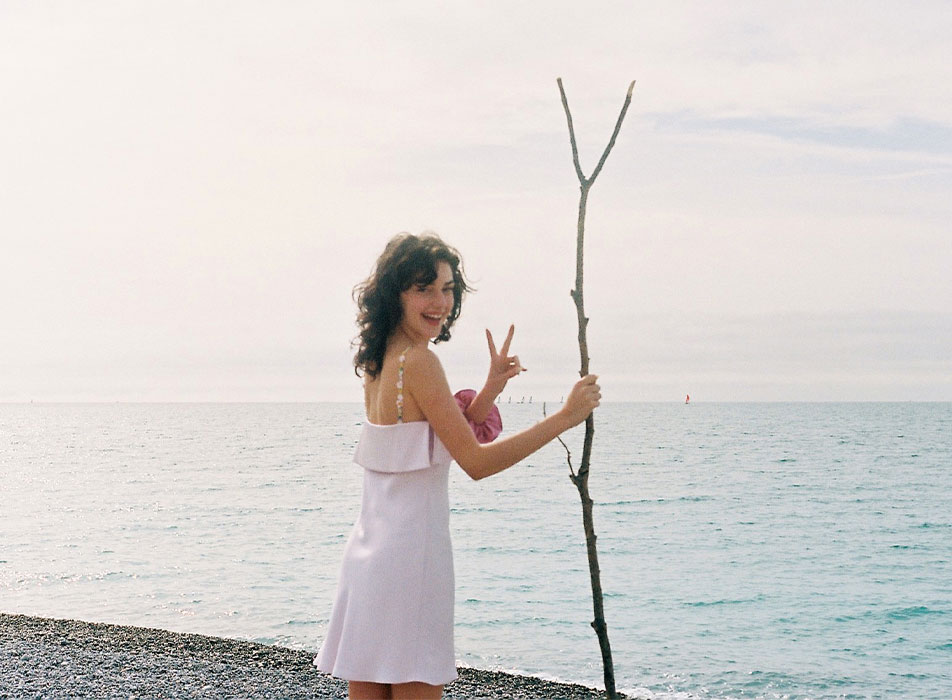
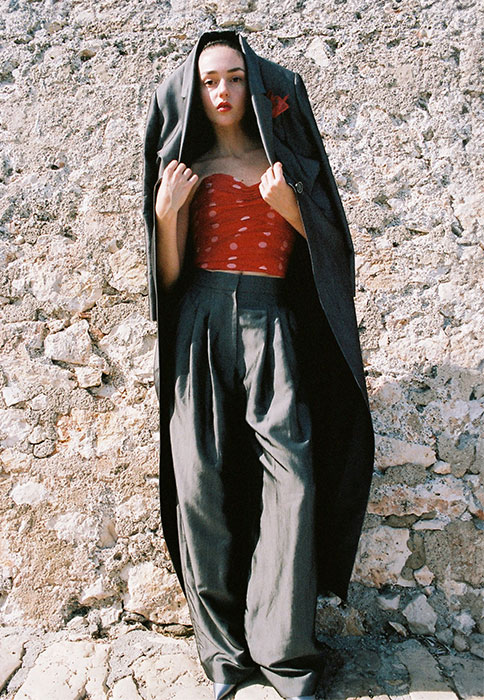